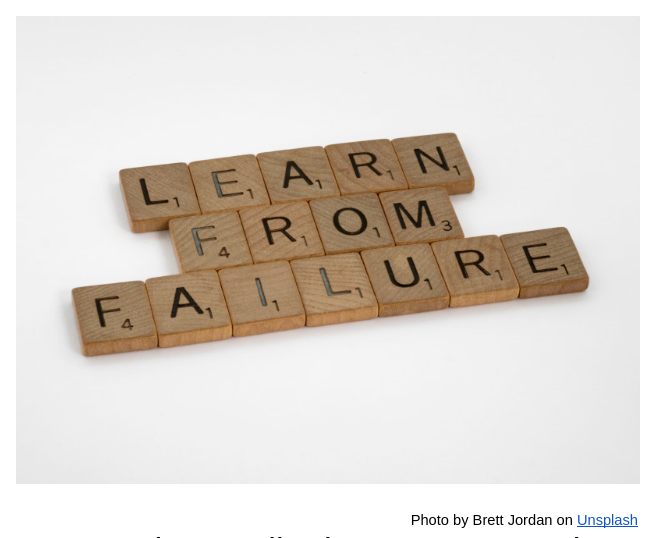
Get Ready to Fail: The 3-Step Learning Cycle of Prototyping
By Mike Rainone
In the early 1900s, Thomas Edison and his researchers were trying to develop a new kind of battery. They had been working on the problem for more than five months when Edison’s long-time associate Walter S. Mallory came to visit.
As Mallory recounted, he found Edison at a long bench covered with hundreds of test cells. The researchers had done more than 9,000 experiments with such cells, but still they had not found a working solution.
“Isn’t it a shame,” Mallory said, “that with the tremendous amount of work you have done you haven’t been able to get any results?”
Edison turned and shot back, “Results! Why, man, I have gotten a lot of results! I know several thousand things that won’t work.”
Over the years, this anecdote has evolved into the famous quote: “I have not failed. I’ve just found 10,000 ways that won't work.”
In innovation, failure is not just unavoidable, but desirable. You want to fail, because failure is how you learn. If everything works, it’s not actually as helpful, because you don’t necessarily know why something worked. It could have been a fluke. Under what conditions won’t it work? You don’t know.
Of course, anyone can create prototypes that fail. The real talent is finally landing on that 10,001st attempt that works. This 3-step cycle of prototyping will help you learn from your efforts so you can adapt and modify, getting closer to a working solution.
Step #1: Gain Knowledge—Test, Test, Test
The entire purpose of a prototype is to test your theories. The first step is thus to gain knowledge: facts and data about what works and what doesn’t work.
Get as much objective, quantitative information as possible. The more hard data you have, the more you can learn. At PCDworks, this is one of the reasons we use LabVIEW so much. LabVIEW is an instrumentation system that allows you to measure a massive number of metrics: displacement, forces, electricity, and so on.
Try to mimic real-world conditions in your tests, and remember that in the real world, conditions are rarely perfect. Your product may have to survive extreme temperatures, long runtimes, user mishandling, and more. So subject your prototype to as much abuse as you expect the device to suffer in real application.
A single successful test does not mean a successful prototype. It only means a successful prototype under a certain set of conditions. So conduct many tests under a variety of conditions to get the most knowledge.
Step #2: Understand Why—Isolate the Problem and Question Every Assumption
Once you have knowledge, you can reach understanding, which means integrating the knowledge to see the whole. Essentially, you know what works and doesn’t work. Now you work to discover why.
Start by isolating the things that do work from the things that don’t. Then do a deep dive on all the parts and pieces, questioning every assumption.
Every aspect of human perception and cognition is a moment to moment building of the world, which allows us to predict what comes next and make the best decisions, minimizing risk and the chances of making a mistake. Our brains are constantly processing information and making hypotheses on a millisecond basis. Every decision we make is a hypothesis, and every hypothesis is built on assumptions, based on (1) prior experience, what we have learned from the past, and (2) the conditions at that exact moment, what we are faced with in the present. If I need eggs, I will turn left out of my driveway because I have a hypothesis, based on experience, that this is the fastest route to a grocery store. That hypothesis is built on assumptions: that the road is not blocked due to construction, that no new stores have opened up closer, that eggs will be in stock, and so on.
When you come up with a concept (a.k.a., a hypothesis) for how to solve your identified problem, you must test that concept. To test a concept, you must build a “prototype.” And I rarely mean a physical prototype, initially. Every prototype should begin with a mathematical model. When a prototype doesn’t work the way you expect, then somewhere there is a hypothesis that is invalid.
The first assumption to question is whether you understand the engineering physics that pertain to the model. Perhaps you miscalculated friction or didn’t factor in the unique properties of a certain material: those are the hypotheses that must be tested as an initial reality check.
If you can’t find any errors, consider redoing tests. A couple of successful tests may have lulled you into a false belief.
By questioning your assumptions, you will eventually unearth the reason for why your prototype doesn’t work.
Step #3: Act with Wisdom—Determine Your Next Steps
So now you have knowledge of what works and doesn’t work, and you have the understanding of why things don’t work. Now it’s time for the final question: What should you do next? This is a question of wisdom.
Wisdom is the judicious application of understanding and knowledge, both the explicit knowledge you have about the current situation and the tacit knowledge you carry with you from years of experience. That tacit knowledge may not be foremost in your mind. It is almost by definition hidden, but it is nevertheless there, ready to come to the fore by the stimulation of all that you come to understand about the current problem. With wisdom, you decide how—or whether—to continue down a particular prototyping path.
First, determine if a solution is even possible. Is there a way to fix the problem you have identified? It may take some time to figure out the solution. Do not give up prematurely. As Edison said, “Many of life's failures are people who did not realize how close they were to success when they gave up.”
If you’re stuck, consult with an expert. You don’t know what you don’t know. An expert brings valuable explicit and tacit knowledge to the table.
Sometimes, though, there is truly not a solution, and you need to go back to the drawing board. Other times, a solution may be theoretically possible but impractical. Remember: this step is about wisdom. Sometimes that means recognizing that a solution is too expensive or will take too much time for the reward to be worth the effort.
Each step of the innovation process should bring you closer to objectively determine whether you go on. As much as possible, take the emotion out of the decision and use wisdom to determine your next steps.
Learn, Adapt, Try Again
I’ll leave you with one final Edison quote: “Genius is 1 percent inspiration, 99 percent perspiration.” That battery he and his developers were working on? They succeeded, patenting and commercializing nickel–iron (NiFe) batteries, which are still in use today.
All things yield to persistence. Prototyping is a process of failure and learning, a continual answering of three questions:
- What works, and what doesn’t work?
- Why doesn’t it work?
- What should you do next?
Through these questions, you learn, adapt, and try again, until you land on that 10,001st attempt that works.